To guarantee label quality control, you need to implement a thorough system that covers regulatory compliance, design, reviews, audits, training, and innovative technologies. Start by establishing a multi-stage review process, conducting regular labeling audits, and training personnel on labeling guidelines. Implement warehouse and laboratory best practices, and utilize technologies like digital proof comparison and automated barcode verification to improve quality assurance. By streamlining quality control processes, reducing human error, and increasing efficiency, you can protect your brand integrity and customer trust. From here, you can investigate more detailed strategies to refine your label quality control system.
Importance of Regulatory Compliance
As you navigate the complex landscape of health supplement labeling, it's crucial to prioritize regulatory compliance to avoid costly mistakes. Failure to comply with labeling regulations can lead to significant legal penalties, fines, and a loss of consumer trust.
The FDA requires health supplements to display accurate nutritional information, allergens, and expiration dates, safeguarding consumer safety and informed choices.
To avoid mislabeling, startups must regularly review and update labels to stay in alignment with evolving regulations. This includes carefully wording claims and benefits on the label to avoid misleading consumers.
Implementing a strong quality control process helps identify compliance issues early, facilitating corrective actions and maintaining adherence to labeling regulations.
Enhancing User Experience Through Design
Effective label design plays a crucial role in improving your brand's credibility and elevating the general user experience. A well-designed label not only showcases your product's features but likewise communicates your brand's values and personality.
By incorporating design principles that prioritize simplicity, clarity, and visual appeal, you can create labels that engage consumers and foster brand loyalty.
Some key elements to take into account when designing labels to improve user experience include:
- Using minimalist design principles to convey simplicity and elegance
- Ensuring clear and visually appealing labels that highlight key product attributes
- Incorporating user feedback to refine label design and improve engagement
- Utilizing consistent font sizes, color coding, and layout to maintain clarity and uniformity
- Creating labels that promote informed purchasing decisions by making crucial information easily accessible
Implementing a Multi-Stage Review Process
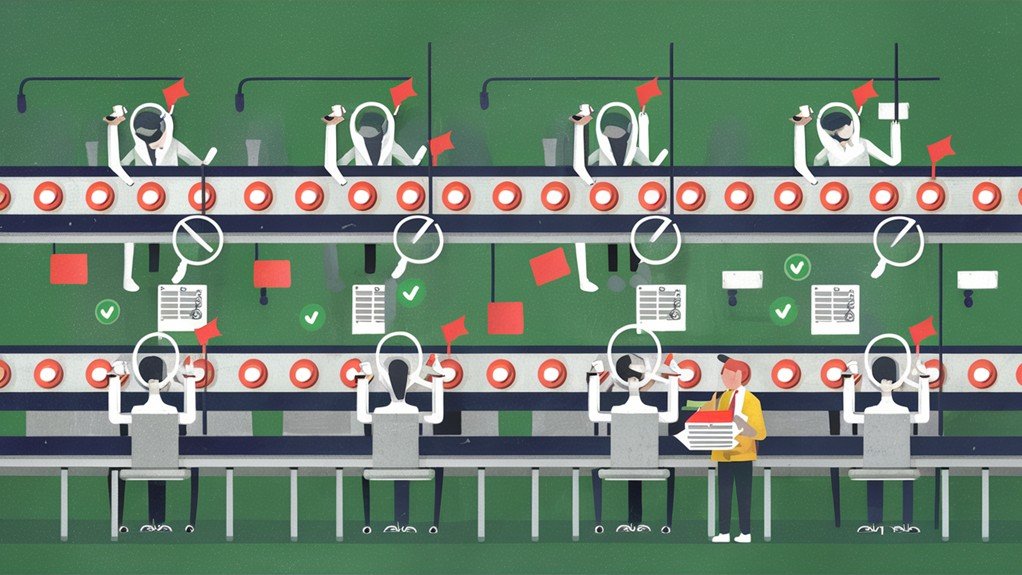
Review Stage | Purpose |
---|---|
Initial Design Validation | Verify design meets regulatory requirements and brand standards |
Content Accuracy Checks | Guarantee accuracy of label content, including text and images |
Final Approvals | Confirm label is ready for production, meeting quality and compliance standards |
Implementing a systematic approach to label reviews not only improves accuracy but likewise fosters a culture of quality and accountability among labeling personnel. Regularly scheduled reviews and updates of labels are crucial to align with evolving regulatory requirements, maintaining compliance and avoiding potential penalties. By implementing a strong review process, you can greatly minimize inconsistencies in labeling, ultimately improving consumer trust and brand credibility.
Conducting Regular Labeling Audits
Your labeling process is only as strong as its weakest link, and that's why conducting regular labeling audits is crucial to guaranteeing the accuracy and compliance of your labels. By doing so, you can identify and rectify any issues before they become major problems.
When conducting regular labeling audits, consider the following key strategies:
- Utilize statistical sampling techniques to guarantee a high level of confidence in labeling accuracy and compliance with regulatory standards.
- Implement a thorough review of labels against established databases to identify discrepancies and improve general labeling quality.
- Use a multi-stage review process to catch errors early, minimizing inconsistencies and guaranteeing accurate labeling.
- Regularly reveal and investigate recurring issues to improve labeling practices and systems.
- Schedule audits at defined intervals to guarantee ongoing quality assurance and compliance with evolving labeling regulations, ultimately enhancing consumer trust.
Training and Educating Labeling Personnel
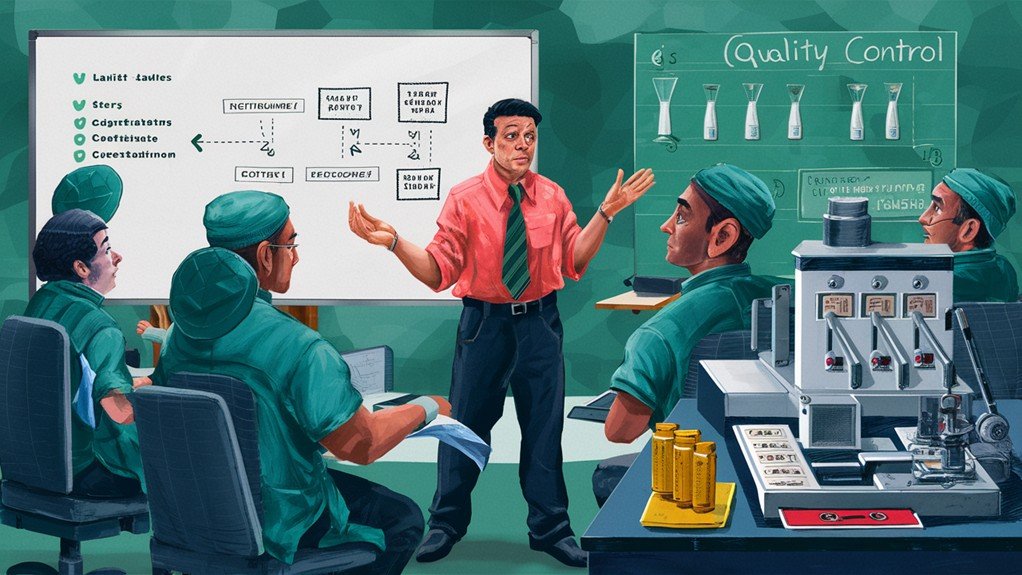
Properly trained labeling personnel are the backbone of a reliable labeling process, and ongoing education is vital to keeping them up-to-date on the latest regulatory compliance requirements. Without it, you risk mislabeling and legal penalties.
To prevent this, you should provide regular workshops that focus on visual hierarchy and labeling guidelines. This will improve your staff's understanding of effective label design, contributing to higher product readability and consumer trust.
Scenario-based training is likewise fundamental, as it equips your labeling staff with practical skills to handle real-world challenges, enhancing their ability to maintain labeling accuracy and quality.
Continuous education fosters a culture of quality and compliance, greatly reducing labeling errors and improving overall precision in product identification.
To guarantee your staff stays updated with evolving industry standards and best practices, include regular assessments in your training programs.
Warehouse Labeling Best Practices and Systems
In the heart of your warehouse operation, effective labeling stands as a vital component, directly influencing the speed and accuracy of your inventory management.
It's imperative to implement labeling best practices and systems that guarantee efficiency, accuracy, and compliance.
To achieve this, consider the following key strategies:
- Implement a consistent labeling format across the warehouse to improve clarity and quick identification, thereby boosting operational efficiency.
- Provide regular staff training on labeling procedures to minimize errors and guarantee compliance with industry standards and safety regulations.
- Conduct periodic audits of warehouse labels to maintain accuracy and condition, preventing discrepancies in inventory management.
- Utilize durable materials that resist environmental factors, such as dust and moisture, to guarantee labels remain intact and legible over time.
- Centralize label management to promote easy access and updates to labeling data, supporting regulatory compliance and consistency across all labeling practices.
Laboratory Labeling Guidelines and Standards
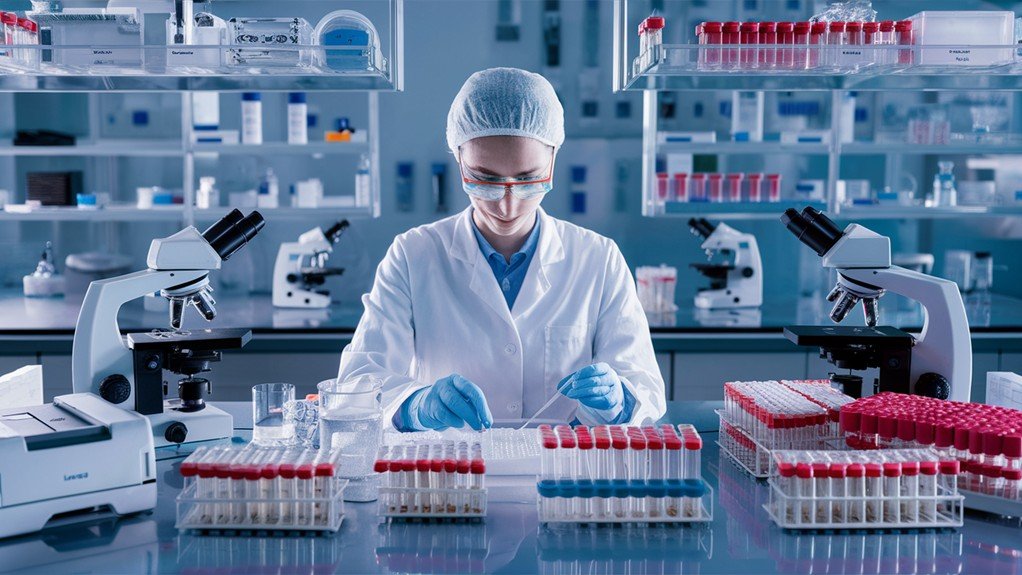
As you venture into the domain of laboratory labeling, it's vital to recognize the paramount importance of adhering to strict regulatory standards. Laboratories must comply with guidelines such as FDA 21 CFR Part 11, which governs electronic records and signatures.
When designing labels, durability is key. Use permanent markers to prevent smudging, especially in wet or humid conditions, and specialty markers for ink-resistant surfaces.
Proper labeling practices are likewise fundamental. Minimize contact with the adhesive side during application to guarantee effective adhesion and prevent labels from falling off. Avoid shortcuts in labeling, as inconsistent shorthand can lead to data loss and miscommunication, jeopardizing research integrity.
Continuous training for labeling personnel on best practices and regulatory updates is vital for maintaining accuracy and compliance in laboratory labeling processes.
Label Quality Control in Manufacturing
By overseeing every stage of label production, you can assure that your labels meet the highest standards of quality. This involves implementing strong quality control measures during manufacturing to prevent errors and inconsistencies.
Some crucial steps to take include:
- Implementing baseline quality control measures, such as QA station checks and real-time monitoring during production, to ascertain labels match approved specifications and reduce printing errors.
- Utilizing advanced technologies like spectrodensitometers for color consistency and digital systems for barcode verification to improve accuracy and scannability.
- Conducting regular audits of internal quality control processes to identify areas for improvement and guarantee compliance with industry standards.
- Engaging with converters about their quality control measures and conducting thorough inspections of shipments to protect brand integrity and customer trust.
- Documenting equipment settings and performing ongoing calibration checks on labeling machinery to prevent misapplication and maintain consistent label quality throughout production runs.
Innovative Technologies for Label Quality Control
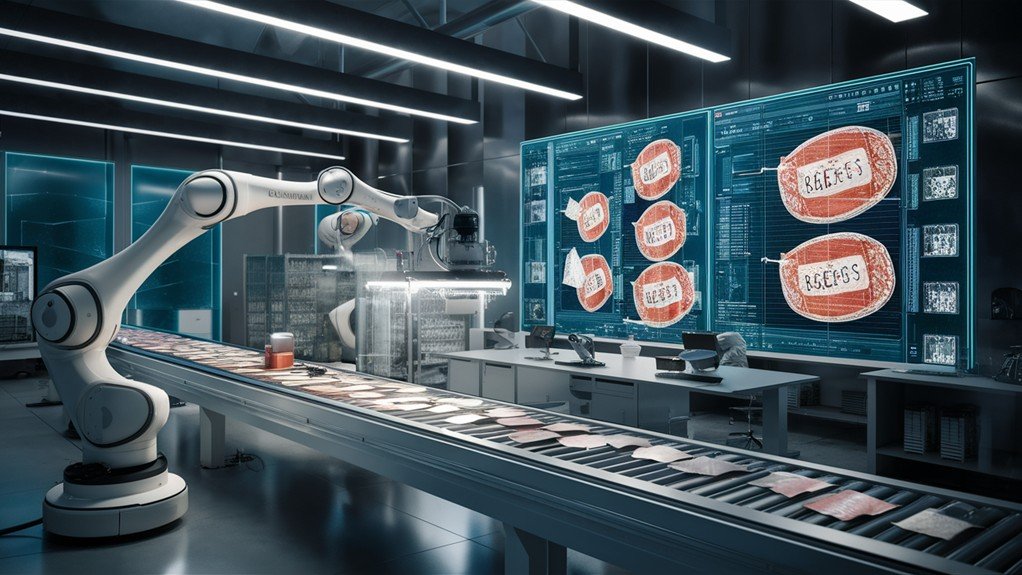
Technology | Benefit |
---|---|
Digital Proof Comparison | Real-time detection of discrepancies between printed labels and approved artwork |
High-Speed Cameras | Immediate comparison of label images to reduce defect chances |
Automated Barcode Verification | Guarantees labels meet retail scannability standards for inventory management and sales tracking |
Implementing automated barcode verification systems guarantees that all labels meet retail scannability standards, which is vital for inventory management and sales tracking. Innovative error mapping techniques document specific print defects to guide rewind operators in addressing issues post-printing, leading to improved comprehensive quality. Regular audits of internal quality control processes are fundamental for identifying areas for improvement and maximizing the efficacy of implemented technologies in label production.
Frequently Asked Questions
What Is the Ideal Frequency for Conducting Quality Control Audits?
You're wondering how often to conduct quality control audits. Ideally, you should schedule them quarterly or bi-annually, depending on your industry and production volume, to guarantee consistency and catch potential issues before they escalate.
How Can We Ensure Label Accuracy in High-Speed Production Lines?
You'll want to implement automated inspection systems and camera verification to catch errors in real-time, ensuring label accuracy in high-speed production lines by detecting defects and anomalies before they reach customers.
What Are the Key Performance Indicators for Label Quality Control?
You'll want to track metrics like defect rate, initial-pass yield, and label accuracy to gauge your label quality control's effectiveness; these KPIs will help you identify areas for improvement and optimize your process for better results.
Can We Use Automation for Label Quality Control in Small Batches?
You're wondering if automation makes sense for small-batch label quality control. While it might seem counterintuitive, you can actually utilize automation tools to streamline even small batches, reducing manual errors and increasing efficiency in the process.
How Do We Balance Quality Control With Production Efficiency Goals?
You're torn between ensuring high-quality standards and meeting production deadlines. To strike a balance, you'll need to identify bottlenecks, streamline processes, and implement efficient quality checks that don't compromise on standards, allowing you to meet efficiency goals without sacrificing quality.
Contents
- 1 Importance of Regulatory Compliance
- 2 Enhancing User Experience Through Design
- 3 Implementing a Multi-Stage Review Process
- 4 Conducting Regular Labeling Audits
- 5 Training and Educating Labeling Personnel
- 6 Warehouse Labeling Best Practices and Systems
- 7 Laboratory Labeling Guidelines and Standards
- 8 Label Quality Control in Manufacturing
- 9 Innovative Technologies for Label Quality Control
- 10 Frequently Asked Questions
- 10.1 What Is the Ideal Frequency for Conducting Quality Control Audits?
- 10.2 How Can We Ensure Label Accuracy in High-Speed Production Lines?
- 10.3 What Are the Key Performance Indicators for Label Quality Control?
- 10.4 Can We Use Automation for Label Quality Control in Small Batches?
- 10.5 How Do We Balance Quality Control With Production Efficiency Goals?