To achieve effective label supply management, you'll need to implement strong inventory control techniques, such as utilizing management information systems for real-time stock tracking, incorporating barcode scanning and RFID tagging, and conducting regular audits. You'll additionally need to manage raw materials and finished goods efficiently by pre-allocating materials, tracking inventory with RFID and barcode scanning, and integrating inventory management with order processing. By implementing these strategies and exploring the areas of warehouse management, quality control, tooling management, and inventory labeling, you'll be well on your way to streamlining your operations and minimizing errors – and that's just the beginning of your expedition to optimizing your label supply management system.
Effective Inventory Control Techniques
Implement effective inventory control techniques to gain a competitive edge in supply management. You can achieve this by utilizing Management Information Systems (MIS) for real-time tracking of stock levels, enhancing accuracy and reducing errors in monitoring inventory movements.
Furthermore, incorporating barcode scanning and RFID tagging allows for efficient tracking and management, as these technologies promote quick identification and retrieval of items, guaranteeing accurate inventory records.
To maintain optimal stock levels, implement rolling stock-takes and periodic audits. This reduces the burden of annual inventory exercises and provides a more accurate view of inventory status.
Employing first-in-first-out (FIFO) principles guarantees proper stock rotation, minimizing the risk of product obsolescence and spoilage, particularly for perishable goods.
Establish clear procedures for stock ordering, receiving, and recording transactions to maintain consistent inventory control practices. This promotes accountability and traceability throughout the supply chain.
Managing Raw Materials and Finished Goods
Effective supply chain management relies on your ability to manage raw materials and finished goods efficiently, as this allows you to pre-allocate materials to jobs and have current stock balances and values readily available for production planning.
To achieve this, you'll need to implement effective tracking and monitoring systems. Consider using RFID tagging and barcode scanning to track raw materials and finished goods in real-time, enhancing traceability throughout the production process.
Regular audits of inventory levels are also vital to maintain accuracy and prevent stockouts or excess inventory, which can lead to increased costs.
Integrating your inventory management system with order processing and production scheduling facilitates timely replenishment of raw materials and efficient fulfillment of finished goods.
Moreover, make certain to track expiry dates on stock items to manage inventory turnover effectively. This guarantees perishable raw materials are used before they expire and finished goods remain sellable.
Warehouse Management and Control Systems
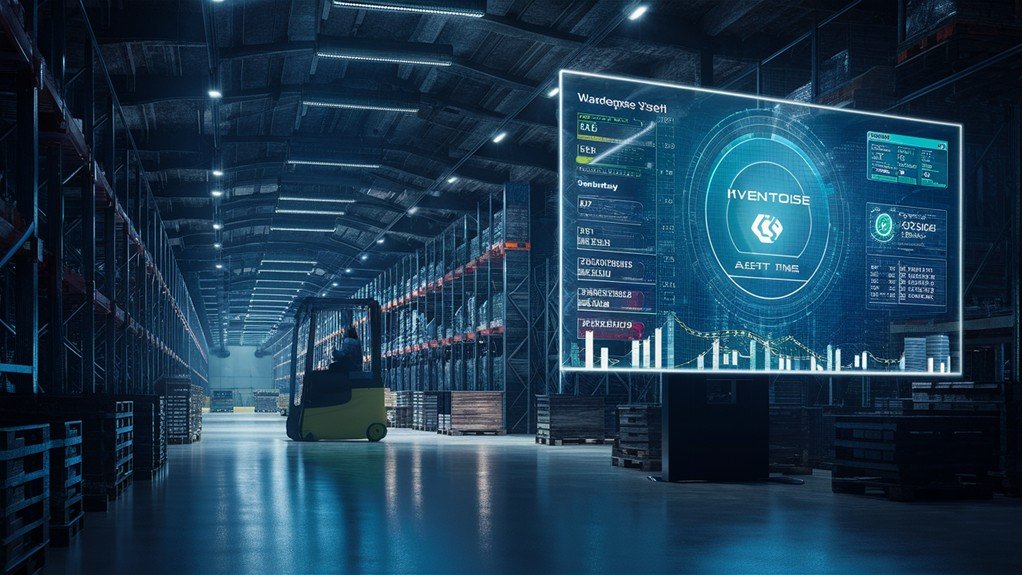
As you oversee the flow of goods within your warehouse, efficient warehouse management and control systems become vital to maintaining a well-oiled supply chain. Implementing first-in-first-out (FIFO) principles guarantees effective stock rotation, minimizing the risk of expired or obsolete inventory. This approach helps you maintain a new and relevant stock, reducing waste and saving resources.
To further improve your warehouse management, consider investing in advanced control systems. These systems provide detailed audit trails, offering an extensive history of stock movements and boosting accountability and traceability.
Mobile WiFi scanners greatly enhance tracking and coordination of warehouse activities, leading to greater operational efficiency and accuracy. Additionally, configurable warehouse layouts promote efficient stock management by optimizing space utilization and improving accessibility to inventory.
Quality Control and Safety Measures
Within your warehouse, maintaining quality control and safety measures is vital to preventing defects, guaranteeing regulatory compliance, and promoting a safe working environment. Implementing systematic quality checks within your inventory system allows you to identify and segregate faulty items, guaranteeing only compliant materials are utilized in production processes.
This thorough approach additionally improves traceability through stock tracking and batch tracking, allowing for quick responses to quality issues.
Regular inspections of tools and storage areas are significant to prevent accidents and maintain safety standards, contributing to a safer workplace environment. Training workers in safe handling practices for inventory reduces the risk of injuries related to heavy or sharp tools, promoting general employee well-being.
Furthermore, implementing built-in reconciliations for adjustments in your inventory system guarantees accurate cost recording and demonstrates a commitment to quality control, improving trust with customers and regulators.
Tooling Management Best Practices
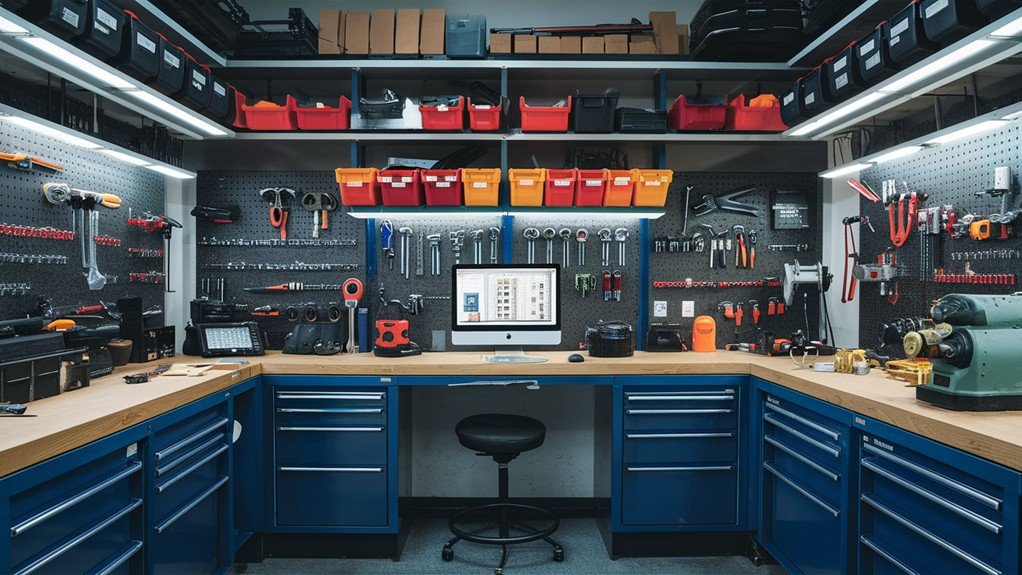
Nearly 80% of production delays are attributed to poorly managed tooling, resulting in considerable losses in productivity and revenue. As you implement effective tooling management best practices, you can greatly reduce the risk of delays and losses.
First, maintain a tooling library with precise documentation for cutting, embossing, and foiling dies. This guarantees that tools are easily accessible and properly managed to avoid operational delays.
Furthermore, regular cleaning, oiling, and inspection of tooling equipment before storage can greatly extend the lifespan of these precision-engineered tools and reduce maintenance costs.
Implementing a systematic approach to track tooling usage and maintenance schedules can improve productivity and minimize the risks associated with tool damage or loss.
Utilizing specialized storage solutions for heavy tools not only enhances safety by reducing the risk of injury but also guarantees that tools are organized and easy to retrieve when needed.
Ultimately, training staff on proper handling techniques for tooling management is crucial to prevent accidents and maintain a safe working environment, ultimately contributing to overall operational efficiency.
Inventory Labeling Strategies and Systems
To optimize the benefits of inventory labeling, consider the following strategies:
- Utilize inventory management software for label creation and syncing, allowing for real-time updates and better visibility.
- Implement automation technologies to further improve the efficiency of inventory labeling processes.
- Train staff on proper labeling procedures and best practices to guarantee adherence to systems, maintaining inventory accuracy and compliance with industry regulations.
Frequently Asked Questions
What Are the 4 Techniques of Inventory Control?
You're looking for inventory control techniques! There are four main ones: Just in Case (JIC) and Just in Time (JIT) manage stock levels, while ABC Analysis prioritizes items and Perpetual Inventory Systems track stock in real-time.
How Do You Control Inventory in Supply Chain Management?
You control inventory in supply chain management by tracking levels in real-time, implementing automated systems, prioritizing items with ABC analysis, conducting regular audits, and building strong supplier relationships to guarantee accuracy, efficiency, and alignment with demand forecasts.
What Is the Best Way to Label Inventory?
You'll want to label inventory by using unique identifiers like barcodes or RFID tags, ensuring durability with plastic sleeves, and incorporating color-codes for easy visual ID; regular audits and staff training are likewise key to maintaining accuracy.
How to Make an Inventory Label?
You start by determining crucial label info, like SKU numbers and expiration dates, then utilize inventory software to generate barcodes or QR codes, and choose durable materials to withstand warehouse conditions.