You can 3D print silicone using specialized technologies like ACEO's printer, which addresses the challenges of silicone's high viscosity and curing time, allowing you to harness its unique properties in your designs. Silicone offers a wide temperature stability range, excellent mechanical properties, and biocompatibility, making it ideal for medical devices, prosthetics, and patient-specific models. When designing for 3D printing silicone, consider factors like viscosity, curing time, and mechanical properties to guarantee successful prints. As you investigate the possibilities of 3D printing silicone, you'll uncover its vast potential for rapid prototyping, customization, and groundbreaking applications.
Properties of Silicone
When working with 3D printing silicone, you'll promptly uncover its impressive range of beneficial properties. The material properties of cast silicone are truly remarkable, boasting excellent mechanical properties that make it an ideal choice for different applications.
One of silicone's standout features is its wide temperature stability range, which spans from -55 to +180 degrees Celsius, making it suitable for use in extreme environments. Moreover, silicone exhibits excellent chemical resistance, ensuring it can withstand exposure to harsh substances without compromising its integrity. Its thermal stability and flexibility also make it an attractive option for applications requiring pliability.
Additionally, silicone's biocompatible properties render it suitable for medical devices and implants, while its durability is strengthened by its resistance to moisture, UV-light, tearing, and chemicals. When printing with silicone, you can expect a watertight seal, making it perfect for various sealing applications.
Collectively, silicone's unique combination of properties makes it a versatile and reliable material for 3D printing.
3D Printing Silicone Methods
You can 3D print silicone using different methods, including Silicone Deposition, Photopolymerization, and Silicone Casting. Each method has its unique benefits and challenges. These methods allow you to create complex designs and prototypes with silicone materials, offering advantages like design freedom and rapid prototyping.
Here are some key benefits of silicone 3D printing methods:
- Design freedom: Create complex geometries and customized designs with silicone materials.
- Rapid prototyping: Quickly test and refine your designs using silicone 3D printing methods.
- Customization options: Tailor your silicone products to specific applications and industries.
- Direct 3D printing: Use technologies like ACEO's 3D printer to directly print silicone materials.
When exploring silicone 3D printing methods, it's essential to consider material considerations like viscosity, curing time, and mechanical properties. By understanding these factors, you can successfully print silicone parts with the desired properties.
Material Considerations
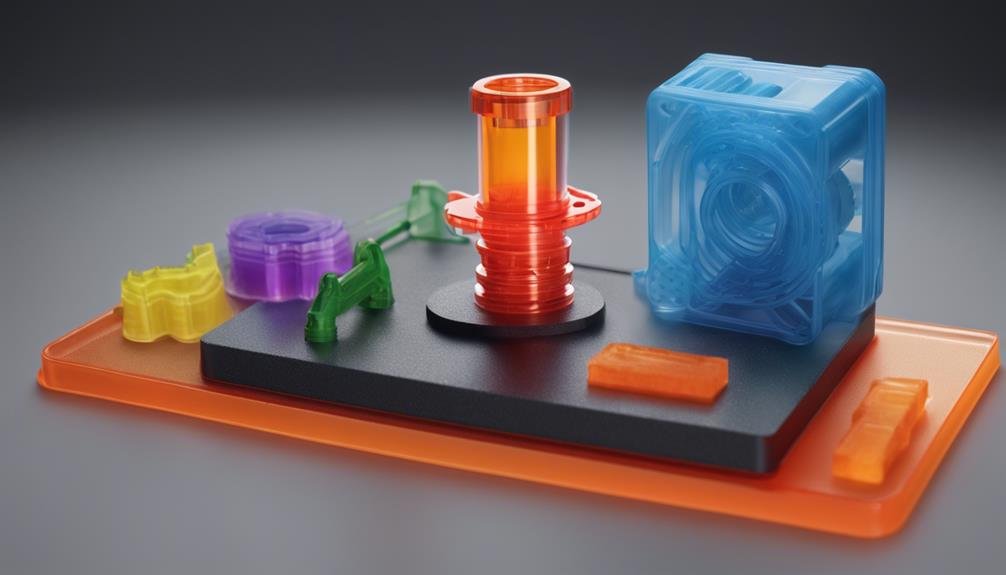
Successfully 3D printing silicone parts requires a deep understanding of the material's unique properties, including viscosity, curing time, and mechanical properties, which greatly influence the printing process. You'll need to take into account these factors to produce high-quality prints.
The viscosity of silicone, for instance, affects the flow rate during extrusion, while curing time dictates the speed of the printing process. Mechanical properties, such as tensile strength and elasticity, impact the final product's durability and flexibility.
However, 3D printing silicone also presents challenges, including limited technology availability and material options. To overcome these obstacles, you'll need to balance cost considerations with material availability.
Precise control of curing is crucial for successful 3D printing of silicone parts. By understanding the unique properties of silicone, you can address these challenges and produce high-quality prints.
With careful material selection and precise curing control, you can harness the full potential of 3D printing silicone.
Advantages and Challenges
With its versatility in material properties, 3D printing silicone offers a multitude of benefits that can improve your designs and prototypes. As you delve into the world of additive manufacturing, you'll uncover the advantages of printing with silicone.
Here are some of the benefits you can anticipate:
- Wide range of material properties: Silicone can be formulated to have a wide range of Shore-A hardness, from 20-60A, providing flexibility in material properties.
- High-quality printed parts: Printed silicone parts have excellent detail and resolution, making them suitable for intricate designs and prototypes.
- Durability and resistance: Silicone parts resist acidic or alkaline environments, high temperatures, moisture, tearing, UV-light, and wear, ensuring durability.
- Cost-effective manufacturing: Silicone provides a cost-effective solution for prototyping and production, with moderate costs compared to other options, saving time and money in the long run.
Applications of 3D Printed Silicone
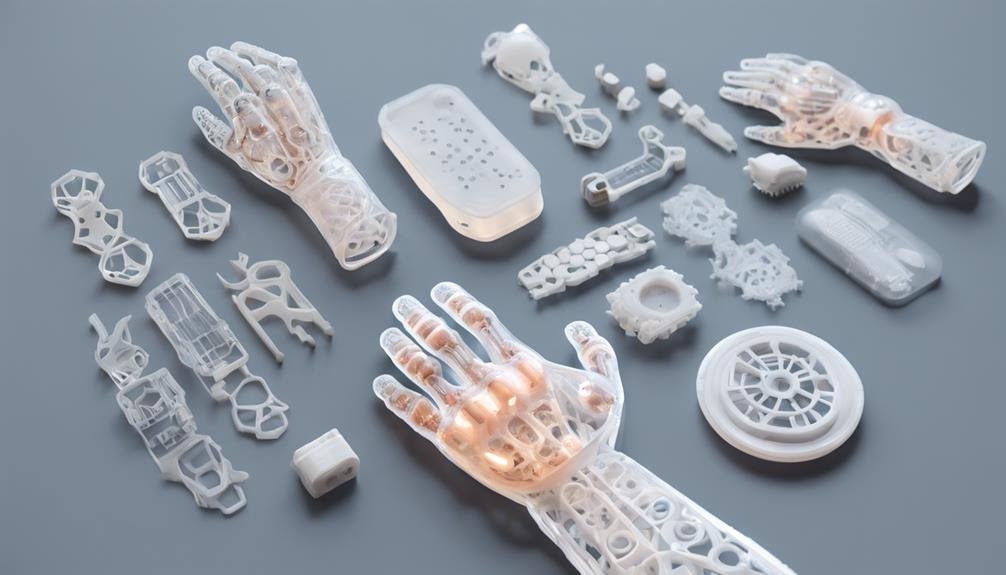
Beyond its advantages, 3D printed silicone's unique properties have led to its adoption in a wide range of industries and applications. You can find printed silicone parts in medical devices, prosthetics, and patient-specific models, where biocompatibility and flexibility are vital.
In the automotive and aerospace industries, customized manufacturing of 3D printed silicone parts takes advantage of its thermal stability, durability, and temperature resistance. Consumer products, such as wearable devices, kitchenware, and toys, also benefit from the material's flexibility and design versatility.
The ability to 3D print silicone enables rapid prototyping, complex geometries, and customized designs in diverse industries. This versatility has opened up new possibilities for custom manufacturing, where unique properties like temperature resistance and flexibility are important.
As you investigate the applications of 3D printed silicone, you'll uncover its potential in different 3D printing applications, from medical devices to consumer products. With its unique combination of properties, 3D printed silicone is poised to revolutionize industries and transform the way we design and manufacture products.
Frequently Asked Questions
What Materials Cannot Be 3D Printed?
You'll find that certain materials, like metal alloys, radioactive materials, biological tissues, explosive compounds, toxic chemicals, high-temperature ceramics, fiber optics, liquid crystals, rare earth magnets, and delicate fabrics, are still off-limits to 3D printing due to technical limitations.
Does Silicone Stick to 3D Printed Parts?
You'll find that silicone adheres well to 3D printed parts, thanks to its tacky nature, but you can improve bonding by optimizing printing surfaces, part geometry, and surface treatments to achieve strong bonds and reliable material interactions.
Does PLA React With Silicone?
You'll be relieved to know that PLA, composed of renewable resources, doesn't react with silicone due to its chemical properties, forming no strong chemical bonds, and its low printing temperatures prevent thermal degradation, ensuring a clean release.
Is There Anything Illegal to 3D Print?
When 3D printing, you must avoid copyright infringement, patent violations, and illegal designs, like firearm restrictions, counterfeit products, and banned objects, as these can lead to serious legal consequences and unethical printing of forbidden artifacts.
Conclusion
Having delved into the world of 3D printing silicone, you've witnessed the unique properties of this versatile material, the different methods for printing it, and the material considerations that come into play.
You've also learned about the advantages and challenges of working with 3D printed silicone, along with its diverse applications.
With this knowledge, you're now equipped to leverage the potential of 3D printed silicone in your own projects, leveraging its flexibility, durability, and biocompatibility to create creative solutions.