In terms of outdoor labeling, UV-resistant labels are a must-have to guarantee your labels remain durable and legible in spite of harsh sunlight and environmental exposure. You need labels that can withstand the elements, from construction sites to automotive parts, packaging, and electronics. Polyester, vinyl, and polypropylene (BOPP) are common materials used for UV protection, each offering unique benefits. By incorporating additives like UV absorbers and stabilizers, labels can maintain their integrity and visual appeal. From understanding UV resistance to choosing the right material, you'll want to investigate the different applications, benefits, and manufacturing processes to get the most out of your UV-resistant labels, and there's more to examine on this topic.
Understanding UV Resistance
When evaluating UV resistance, accelerated weathering tests are commonly used to simulate outdoor conditions.
These tests help manufacturers meet specific performance standards and guarantee their labels can withstand harsh environments.
By understanding UV resistance, you'll be better equipped to select the right labels for outdoor applications.
This knowledge will directly impact the longevity and effectiveness of your labeling solution.
Consider the importance of UV resistance when choosing labels for outdoor use, and look for materials that have undergone rigorous testing to confirm their performance and durability.
Importance of UV Resistant Materials
Through prolonged exposure to the elements, outdoor labels, coatings, and packaging materials are constantly at risk of degradation and discoloration caused by UV light. This degradation can lead to a decrease in product performance, safety issues, and a negative impact on your brand's reputation.
That's why it's vital to use UV-resistant materials that can withstand harsh sunlight. You need to guarantee the materials you use can maintain their integrity and performance over time.
UV-resistant materials are designed to do just that. By incorporating UV absorbers, inhibitors, or stabilizers during manufacturing, these materials can resist degradation and discoloration. This is especially significant in industries like construction, automotive, and electronics, where product performance and safety are fundamental.
Additionally, regulatory compliance may require specific UV resistance standards, so it's imperative to adhere to these guidelines to avoid legal repercussions. By using UV-resistant materials, you can assure your products maintain their quality and performance, even in harsh outdoor environments.
Applications of UV Resistant Materials
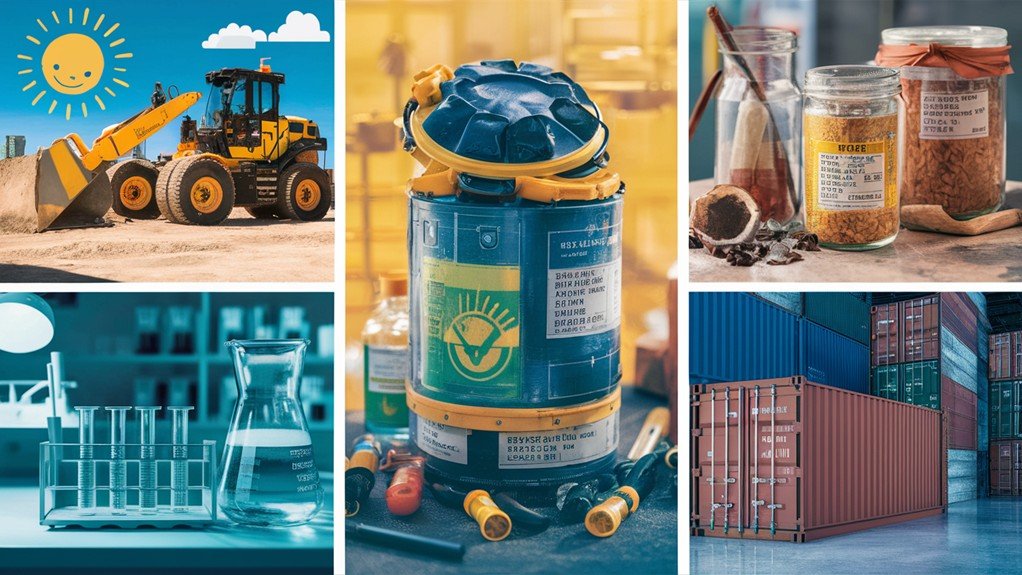
Your outdoor products and packaging rely on UV-resistant materials to perform their best. These materials play an essential role in preventing fading and damage from prolonged sunlight exposure, ensuring the longevity of product labeling.
Industry/Application | Products/Packaging | Benefits of UV Resistance |
---|---|---|
Construction | Roofing, Siding | Maintains structural integrity |
Automotive | Parts, Components | Improves durability and performance |
Packaging | Outdoor Display Materials | Preserves product appearance and information |
Electronics | Sensitive Components | Reduces risk of failure and extends lifespan |
UV-resistant materials are commonly used in numerous industries, including construction, automotive, packaging, and electronics. In construction, UV protection helps maintain the structural integrity of roofing and siding over time. In the automotive industry, these materials protect sensitive components from degradation caused by sunlight, improving durability and performance. For packaging designed for outdoor display, UV-resistant materials preserve product appearance and information against harsh environmental conditions. In electronics, UV-resistant materials safeguard sensitive components from UV light, reducing the risk of failure and extending product lifespan.
Materials for UV Resistant Labels
Beyond the domain of industrial applications, UV-resistant materials take on a more subtle role in the sphere of labeling, where their performance is paramount to conveying critical information.
You'll commonly find UV-resistant labels made from materials like polyester, vinyl, and polypropylene (BOPP), all of which provide excellent protection against UV radiation and environmental wear.
Polyester labels, known for their exceptional resistance to harsh conditions, are ideal for outdoor applications where prolonged sunlight exposure is a concern.
Vinyl labels, constructed from durable polyvinyl chloride (PVC), maintain legibility and vibrancy even after extended exposure to UV rays as a result of their high resistance to fading.
Polypropylene labels offer a flexible design that conforms well to curved surfaces while additionally being UV-resistant, making them suitable for multiple labeling needs in outdoor settings.
To improve their UV resistance, additives like UV absorbers and stabilizers are often integrated into the manufacturing process of these materials, guaranteeing long-lasting performance in outdoor applications.
How UV Resistant Labels Work
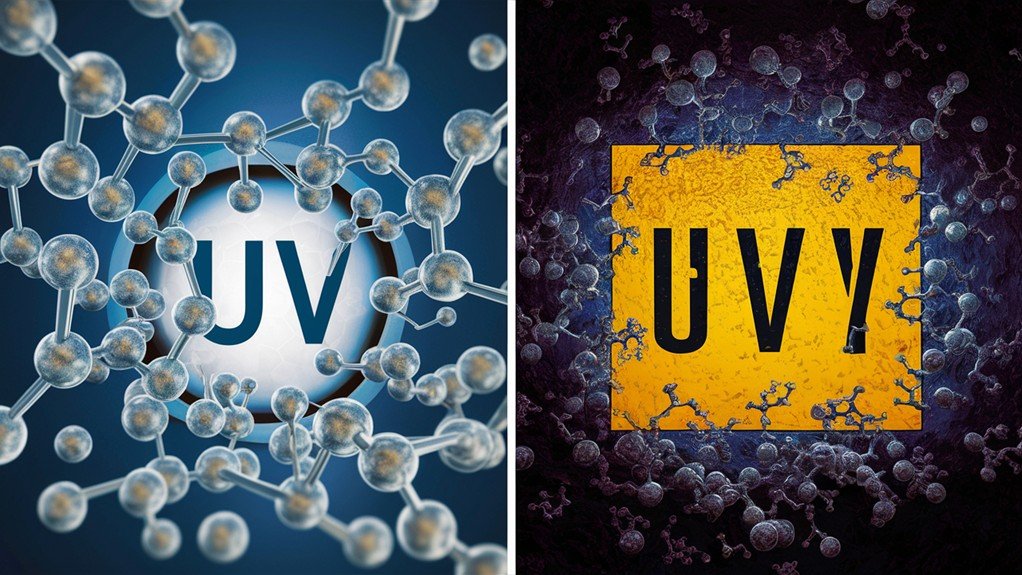
Reliability is key regarding conveying critical information through labeling, and UV-resistant labels deliver on that promise. You might wonder how they achieve this. The secret lies in their manufacturing process, where additives like UV absorbers and stabilizers are incorporated to absorb UV light and convert it into low-level heat, preventing material degradation.
These additives allow the labels to maintain their integrity and visual appeal by resisting fading and discoloration, ensuring longevity even when exposed to harsh sunlight.
To verify their UV resistance, accelerated weathering tests are conducted, simulating real-world conditions to evaluate their performance.
High-performance inks and coatings are specifically formulated to withstand extensive UV exposure without deteriorating or losing legibility. This makes UV-resistant labels suitable for diverse applications, including outdoor signage, automotive parts, and packaging materials that require durability against UV radiation.
Benefits of UV Resistant Labels
By safeguarding against degradation and discoloration, UV-resistant labels greatly extend their lifespan in outdoor environments, giving you peace of mind regarding conveying vital information.
This increased durability guarantees that your labels remain legible and visually appealing, even when exposed to harsh sunlight, moisture, and chemicals. Consequently, you can confidently use UV-resistant labels in diverse applications, such as outdoor signage, automotive, and packaging materials, where maintaining label integrity is essential.
Moreover, UV-resistant labels help you meet regulatory compliance in industries where outdoor labeling is subject to specific standards. By choosing labels that can withstand the elements, you can avoid costly re-labeling and confirm your products meet the required standards.
With UV-resistant labels, you can enjoy the benefits of longer label lifespan, reduced maintenance, and increased customer satisfaction. By investing in high-quality UV-resistant labels, you're investing in the long-term success of your business.
Choosing the Right Label Material
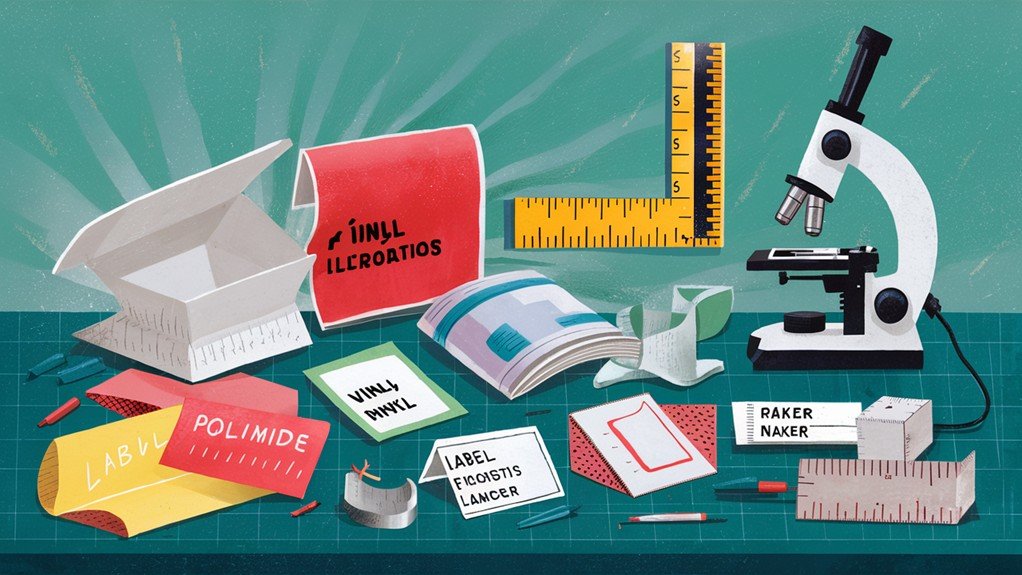
In relation to ensuring the longevity of your UV-resistant labels, selecting the right material is crucial.
You'll want to take into account the specific application requirements, as different materials excel in diverse environments. For outdoor applications, vinyl labels constructed from durable polyvinyl chloride (PVC) are an excellent choice, offering excellent resistance to moisture, UV rays, and extreme temperatures.
For harsh environmental conditions, polyester labels are ideal, providing exceptional resistance to water, chemicals, and UV radiation.
Polypropylene (BOPP) labels, made from a tough plastic material, are flexible and resistant to water, oil, and chemicals, making them a versatile option for numerous surfaces.
When choosing a label material, keep in mind the following key factors:
- Environmental conditions: Will the label be exposed to water, chemicals, or extreme temperatures?
- Surface type: Will the label be applied to a smooth, irregular, or curved surface?
- Adhesive requirements: Do you need a permanent or removable adhesive, and what level of bond strength is required?
Manufacturing and Testing UV Resistant Products
Manufacturing UV-resistant products involves incorporating specialized additives into polymers during production to improve their ability to withstand the harsh effects of UV light exposure.
These additives, such as UV absorbers and stabilizers, play a vital role in enhancing the durability of your labels.
To confirm the UV resistance of your labels meets industry standards, manufacturers employ accelerated weathering tests.
These tests simulate long-term exposure to sunlight and environmental conditions, allowing manufacturers to evaluate the performance of their products under harsh conditions.
Industry standards define specific UV resistance levels required for diverse applications, confirming consistency and reliability in the performance of UV-resistant products.
Throughout the manufacturing process, quality control measures are implemented to verify the effectiveness of UV protection and maintain product integrity.
Future Trends in UV Resistance
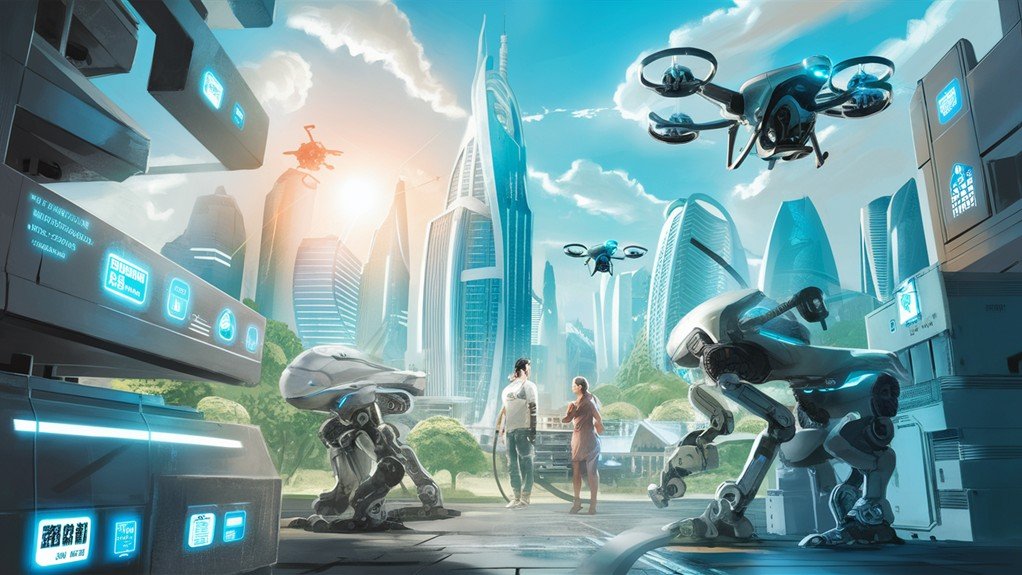
Several key developments are poised to shape the future of UV resistance, transforming the way you think about label durability.
As you look to the horizon, you can expect significant advancements in sustainable materials, advanced UV stabilizers, and innovative nanotechnology. These emerging trends will redefine the possibilities for outdoor applications and beyond.
Here are three exciting developments to watch:
- Eco-friendly UV resistance: Research is underway to create biodegradable materials that possess UV resistance properties, aligning with environmental sustainability goals.
- Nanotech integration: The use of nanotechnology is expanding, leading to improved UV protection through innovative materials that can be integrated into diverse products.
- Broader applications: Industries are exploring broader applications for UV resistance, including textiles and electronics, to protect sensitive components from harmful UV exposure.
These advancements won't only improve performance but also contribute to a more sustainable future.
As you consider the implications of these trends, you'll realize that the possibilities for UV-resistant labels and materials are vast and exciting.
Frequently Asked Questions
What Materials Are UV Resistant?
You're looking for materials that can withstand the sun's harsh rays, right? Well, you'll be happy to know that vinyl, polyester (PET), and polypropylene (BOPP) are all UV-resistant materials, ensuring your labels stay vibrant and legible even in direct sunlight.
How Does UV Affect Labels?
You've probably noticed how UV exposure causes labels to fade, losing their vibrancy and legibility over time, especially outdoors where sunlight is intense, leading to a dull, worn-out appearance that can compromise their effectiveness.
What Are UV Resistant Properties?
You're wondering what UV resistant properties are. Well, they allow materials to withstand prolonged UV exposure without degrading or losing their structural integrity, thanks to additives that convert harmful UV energy into low-level heat.
What Does UV Resistant Mean?
You're wondering what "UV resistant" means? It means you need materials that can withstand harsh sunlight without degrading or discoloring, so your labels stay legible and vibrant, even when exposed to intense ultraviolet light over time.
Contents
- 1 Understanding UV Resistance
- 2 Importance of UV Resistant Materials
- 3 Applications of UV Resistant Materials
- 4 Materials for UV Resistant Labels
- 5 How UV Resistant Labels Work
- 6 Benefits of UV Resistant Labels
- 7 Choosing the Right Label Material
- 8 Manufacturing and Testing UV Resistant Products
- 9 Future Trends in UV Resistance
- 10 Frequently Asked Questions