In 3D printing metals, the composition of the alloy plays a crucial role in strength. Rapid cooling during printing impacts crystal structure and subsequent strength. Testing methods such as tensile, compression, impact, hardness, and fatigue tests guarantee reliability. Control of alloy composition is essential for consistent strength. Factors affecting printed metal strength include material selection, printing parameters like layer height, and post-processing techniques like heat treating. Improve strength by optimizing part design. Case studies show that post-processing methods boost mechanical properties. 3D printed stainless steel can be up to 3 times stronger than conventionally manufactured parts, offering advanced strength with controlled material structure.
Understanding Metal 3D Printing Strength
To understand the strength of 3D printed metal, consider the interplay of material composition, printing parameters, and post-processing techniques. These factors all contribute to the final strength and durability of the 3D printed metal part. Material composition determines the intrinsic properties of the metal, while printing parameters such as temperature and speed affect the internal structure and integrity of the printed part. Post-processing techniques, such as heat treatment or surface finishing, can further enhance the mechanical properties of the 3D printed metal. With the development of affordable metal printing technology, more industries are able to take advantage of the strength and versatility of 3D printed metal parts for various applications.
Metal 3D printing involves carefully selecting the materials composition to guarantee the best strength in the final product. The alloy composition plays a pivotal role in determining the mechanical properties of the printed metal parts.
During the printing process, rapid cooling occurs, influencing the crystal structure of the material and consequently affecting its overall strength and durability.
To evaluate the strength of these components, different testing methods such as tensile, compression, impact, hardness, and fatigue tests are employed. These rigorous testing procedures are vital for ensuring the reliability and performance of 3D printed metal parts.
In addition, controlling the alloy composition is critical for achieving consistent and robust metal components.
Factors Affecting Printed Metal Strength
Material selection, printing parameters, part design considerations, and post-processing techniques all play pivotal roles in determining the strength of 3D printed metal components.
Materials Selection:
The mechanical properties of the chosen material greatly influence the strength of the final 3D printed metal part. Factors such as tensile strength, yield strength, and ductility must be carefully evaluated during material selection.
Printing Parameters:
Variables like layer height, infill density, and printing speed are critical in achieving the desired strength in 3D printed metal parts. Ideal parameter settings can improve the mechanical properties of the final component.
Part Design Considerations:
The geometry, orientation, and features of the part impact its strength. Careful consideration of these design aspects is vital to secure the structural integrity of the printed metal component.
Post-Processing Techniques:
Techniques like heat treating and chemical smoothing can boost the strength of 3D printed metal parts. Proper post-processing is key to improving mechanical properties and the performance of the part.
Testing Methods for Metal Prints
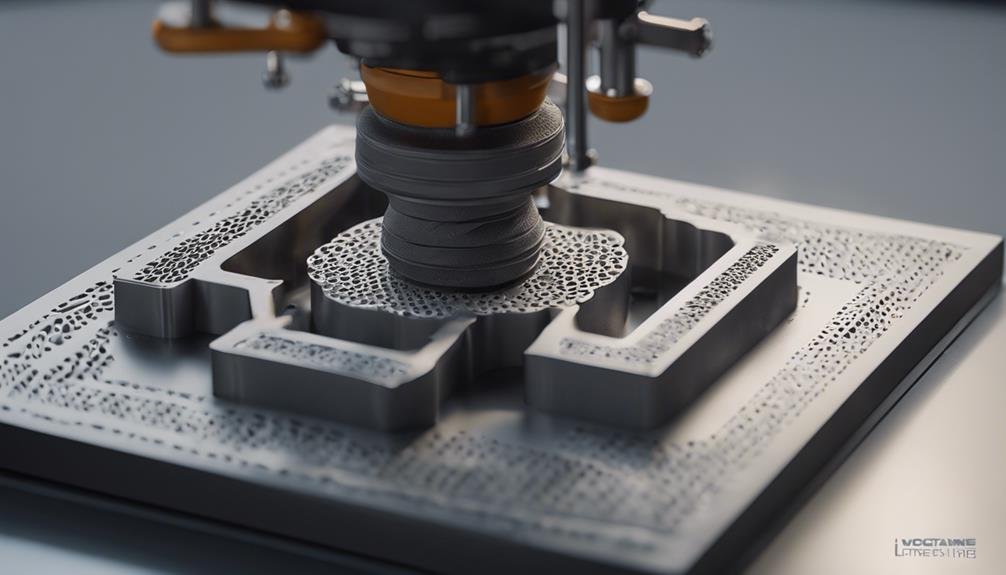
Considering the strength of 3D printed metal components, understanding the testing methods for metal prints is important for evaluating their performance and durability.
Tensile testing is a common method that involves applying tension to a sample until it fractures, allowing the measurement of its ultimate tensile strength.
Compression tests, on the other hand, assess how well a 3D-printed metal component can withstand crushing forces, providing insights into its compressive strength.
Impact testing plays a significant role in determining a metal print's toughness by measuring its resistance to sudden loading or impact.
Hardness tests help evaluate the material's resistance to deformation, which is indicative of its general strength and wear resistance.
Additionally, fatigue testing is crucial for examining the endurance limit of 3D-printed metal under repeated stress, offering valuable information on its long-term durability.
Improving Metal Print Strength Strategies
Improving the strength of metal prints involves implementing strategies that optimize material selection and printing parameters. To achieve this, consider the following key points:
- Material Selection: Choose metal materials based on their specific mechanical properties, such as tensile strength, yield strength, and ductility. Different metals offer varying levels of strength, impacting the final print's durability.
- Printing Parameters: Adjust factors like layer height, infill density, and printing speed to boost the structural integrity of the metal print. These parameters directly influence the strength and quality of the final product.
- Part Design Considerations: Optimize part geometry, orientation, and features to improve print strength. Proper design can prevent weak points and ensure that the metal print can withstand intended loads and stresses.
- Post-Processing Techniques: Utilize methods like heat treating and chemical smoothing to improve the mechanical properties of the printed metal. Post-processing can help increase the strength and durability of the final component.
Case Studies in Strength Improvement
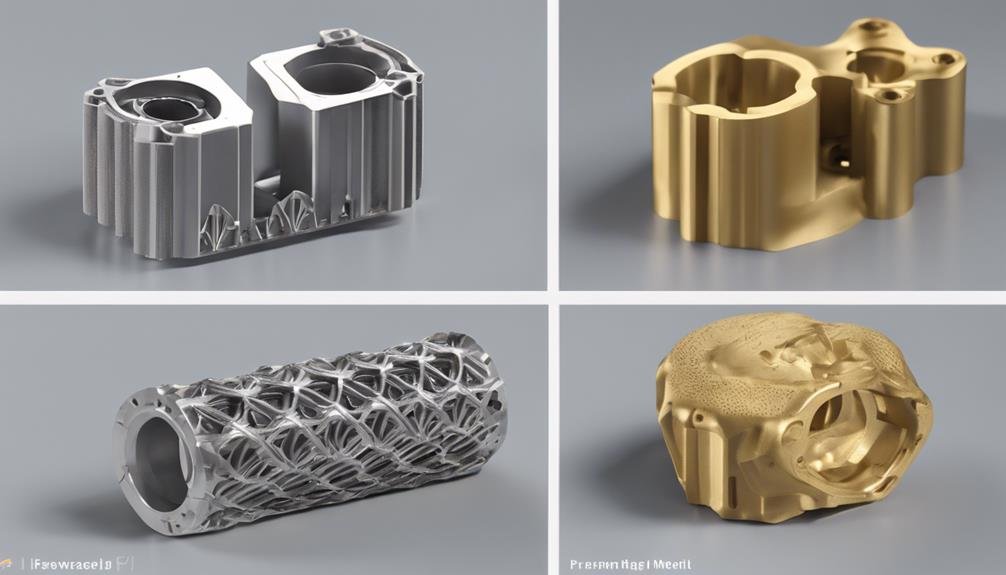
To showcase the practical application of strategies for improving metal print strength, examining case studies in strength improvement through post-processing methods like heat treating is essential. These case studies offer valuable insights into the effectiveness of different techniques in boosting the strength of 3D printed metal parts. By implementing strategic post-processing methods, significant improvements in strength properties can be achieved, leading to more durable and reliable components.
Below is a table summarizing key aspects of case studies in strength improvement:
Aspect | Description |
---|---|
Post-processing | Heat treating and other methods used to augment the strength of 3D printed metal parts |
Strength Enhancement | Demonstrates the increase in mechanical properties after post-processing interventions |
3D Printing Techniques | Influence of printing methods on the strength improvement outcomes |
Material Selection | Impact of material choice on the effectiveness of post-processing for strength augmentation |
Testing Methods | Various tests conducted to evaluate the improved strength properties of 3D printed metal parts |
Analyzing these case studies provides valuable knowledge for engineers and manufacturers seeking to optimize the strength of their 3D printed metal components.
Materials and Printing Parameters
Selecting appropriate materials and optimizing printing parameters are pivotal factors in strengthening 3D-printed metal parts.
To improve the strength and durability of your metal printing, consider the following:
- Material Selection: Choose materials like titanium or steel known for their robustness in additive manufacturing. Consult with a materials scientist to determine the best option for your specific requirements.
- Printing Parameters: Optimize settings such as infill density, pattern, and temperature to guarantee the structural integrity of your parts. Adjusting these parameters can greatly impact the final strength of your 3D-printed metal components.
- Complex Parts: When designing intricate or complex parts, pay attention to load application direction to optimize their strength. Proper orientation during printing can prevent weak points and improve overall resilience.
- Print Speed: While faster print speeds may seem appealing, slow and steady printing can actually strengthen the robustness of your metal parts. Balancing speed with quality is crucial for achieving strong and durable components.
Comparing 3D Printed to Traditional
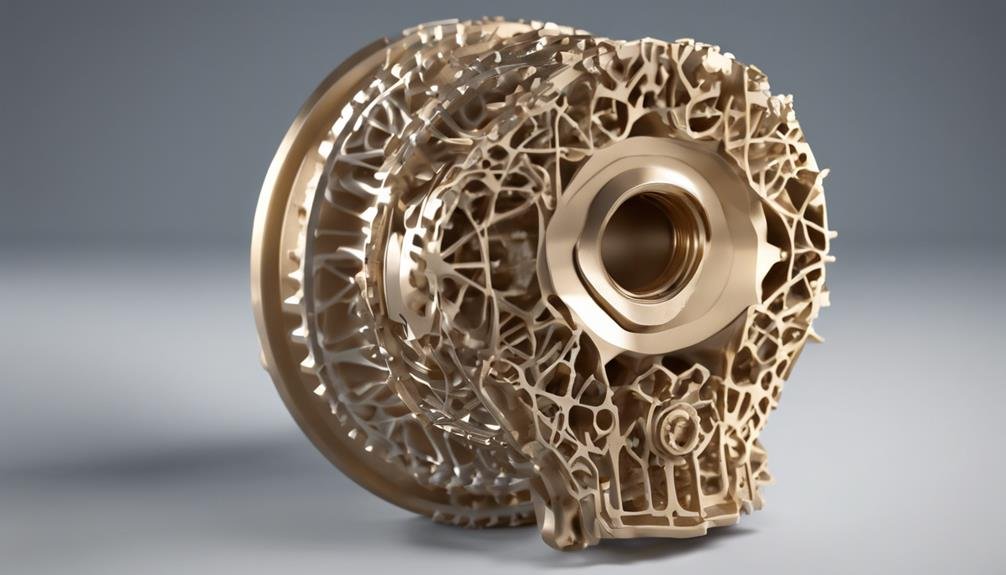
When comparing 3D printed metal parts to traditionally manufactured components, the importance and advantages of additive manufacturing become evident. 3D printing allows for the creation of parts with up to three times the strength of conventionally manufactured ones. The dense layers and microscopic structures of 3D printed metals play a vital role in preventing fractures while still maintaining flexibility, a feat that is challenging to achieve with conventional manufacturing methods. Rapid cooling processes and precise control of material structure further improve the strength of 3D printed metal components, making them highly desirable for different industrial applications.
To provide a clearer comparison, let's look at a table showcasing the strengths of 3D printed stainless steel parts versus those manufactured through conventional methods:
Strength Aspect | 3D Printed Stainless Steel | Conventionally Manufactured Parts |
---|---|---|
Strength | Up to 3x stronger | Standard strength |
Fracture Resistance | Improved | More prone to fractures |
Material Structure | Controlled at nanoscale to micron scale | Less controlled and uniform |
Understanding these differences emphasizes the superior qualities of 3D printed metal parts, particularly regarding strength and structural integrity.
Frequently Asked Questions
How Strong Are 3D Printed Metals?
In terms of metal durability, 3D printing excels. The process improves material strength through precise layer adhesion and structural integrity. Stress testing consistently proves that 3D printed metals match the strength of conventionally produced ones.
What Is the Strongest Type of Metal 3D Printing?
For the most effective type of metal 3D printing, investigate cutting-edge structures with high-performance metal composites. Improve material properties and mechanical strength through advanced additive manufacturing techniques. Tailor alloy compositions for best results in creating robust metal parts.
How Strong Is 3D Printed Titanium?
3D printed titanium boasts impressive strength due to its exceptional properties. The 3D printing process improves structural integrity, ensuring material durability. This metal's comparative strength makes it a top choice for aerospace and medical applications, surpassing traditional manufacturing capabilities.
How Strong Can 3D Printed Parts Be?
3D printed parts can exhibit exceptional strength due to their unique material properties and precise design considerations. Layer adhesion, post-processing techniques, and stress testing further improve strength. This technology finds applications in diverse industries.
Conclusion
In summary, understanding the importance of 3D printed metal is essential for successful manufacturing applications.
Factors such as material properties, printing parameters, and post-processing techniques all play a role in determining the final strength of a metal print.
By utilizing appropriate testing methods and implementing strategies to improve print strength, manufacturers can achieve high-quality, durable metal parts.
The continuous advancement in materials and technology in the field of metal 3D printing offers exciting opportunities for innovation and efficiency in different industries.
Contents
- 1 Understanding Metal 3D Printing Strength
- 2 Factors Affecting Printed Metal Strength
- 3 Testing Methods for Metal Prints
- 4 Improving Metal Print Strength Strategies
- 5 Case Studies in Strength Improvement
- 6 Materials and Printing Parameters
- 7 Comparing 3D Printed to Traditional
- 8 Frequently Asked Questions
- 9 Conclusion